Система планирования производства в машиностроении
ПО для распределения производства на участках лазерной и плазменной резки листового металла.
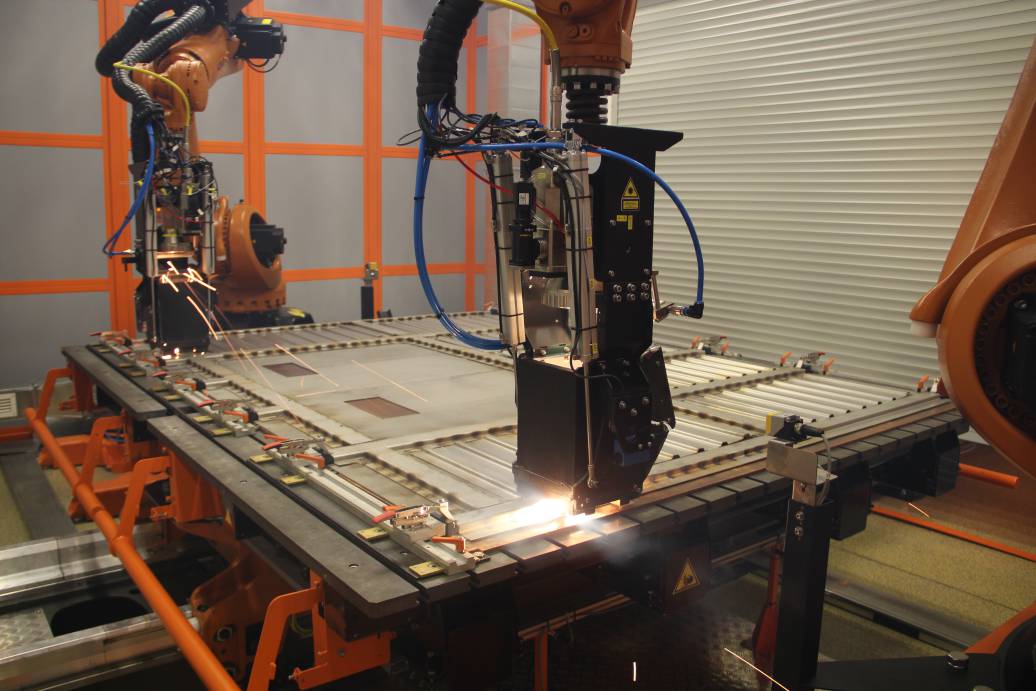
Задача
Цель создания ПО - оптимизация формирования производственной программы для доступных производственных площадок с учетом технологических особенностей лазерной и плазменной резки металла.
ПО призвано обеспечить высокий коэффициент использования материала (КИМ) для карт раскроя, входящих в производственную программу, что позволит снизить объем производственных отходов. Учитывая повышение цен на материалы, снижение расхода сырья позволяет значительно повысить экономическую эффективность предприятия.
Разрабатываемая система обеспечит:
- Определение целевого КИМ в долгосрочной перспективе;
- Совмещенное планирование долгосрочных, спотовых и экстренных заказов;
- Распределение заказов по группам взаимозаменяемости оборудования с учетом режимов работы оборудования, графиков планово-предупредительного ремонта и автономного обслуживания;
- Расчет экономического эффекта оптимизации производственной программы с учетом затрат на логистику и изменения КИМ.
Решение
Система позволит перераспределять заказы на производство отдельных деталей между предприятиями одного холдинга так, чтобы на каждом из них расположение деталей на листе раскроя во время выполнения каждой операции было оптимальным.
Таким образом повышается коэффициент использования материала (КИМ) – краеугольный камень при оптимизации производства в машиностроении. При повышении КИМ снижается уровень отходов производства, что в свою очередь уменьшает издержки и повышает его экономическую эффективность. Учитывая увеличивающийся спрос на сырье, повышение среднего КИМ даже на несколько процентов приведет к серьезной экономии.
При разработке программного обеспечения используются передовые цифровые и промышленные технологии на стыке нескольких научных дисциплин: прикладной математики, информационных технологий, кибернетики и искусственного интеллекта. Этот набор методов позволяет решать сложные оптимизационные задачи, актуальные не только для научного сообщества, но и для промышленных предприятий.
В настоящий момент разработан и реализован опорный алгоритм, который связывает между собой все части системы и выполняет непосредственную оптимизацию производственной программы. Уже проведены первые испытания, по результатам которых повышение планового КИМ составляет 6–8%.
Алгоритм программы можно разделить на две части:
- Обработка плана потребности в деталях с нескольких производственных площадок и последующая оптимизация распределения деталей по картам раскроя.
- Распределение полученных карт раскроя по производственным мощностям.
Алгоритм обработки плана потребностей в деталях объединяет производственные программы с нескольких площадок и затем делит их на группы по количеству деталей, которое требуется произвести. Полученные группы повторно делятся по типам металла и отправляются в стороннюю систему для раскладки по картам раскроя. Карты раскроя анализируются с точки зрения коэффициента использования материала. «Неудачные» карты раскроя повторно перерабатываются с учетом возможности изготовления в более ранний период или замены материала, если есть такая возможность.
На следующем этапе запускается алгоритм распределения деталей по площадкам, который позволяет учитывать график рабочих смен, время на переналадку оборудования, ремонт и замену оборудования, а также резерв под экстренные заказы. Распределение карт раскроя происходит с учетом технологических особенностей обработки конкретного вида металла и технических особенностей оборудования. Программа потребности распределяется последовательно по доступным производственным мощностям, что позволяет эффективно использовать ресурсы и избегать простоев.
Этапы проекта
В рамках 1 этапа (2021-2022) реализовано:
- разработка базового алгоритма, обеспечивающего распределение заказов согласно основной производственной программе;
- алгоритм учета графика рабочего времени оборудования;
- алгоритм учета различных форматов листов одного типа металла;
- алгоритм учета срочных заказов с последующим перераспределением производственных мощностей.
Первый этап проекта завершен и проходит этап функционального тестирования у заказчика.
В рамках 2 этапа (2022) планируется:
- разработка сервиса для расчета нескольких вариантов производственной программы с учетом выбора параметров для сопоставления результатов;
- интеграция ПО с 1С:ERP в части автоматизированного обмена данными о заказах и полученной производственной программе;
- разработка нового frontend решения для ПО согласно пожеланиям Заказчика.
Технологии
Языки программирования и фреймворки | С#, JavaScript |
САПР | Autonest 18 |
Программные платформы | .net Framework 4.7, AngularJs |
База данных | MySQL |
РИД
Публикации
Ключевые исполнители
Разработка осуществляется объединенным коллективом лабораторий «Цифровое моделирование индустриальных систем» и «Промышленные системы потоковой обработки данных» Центра НТИ СПбПУ в сотрудничестве с членом консорциума Центра НТИ ООО «Тетракуб» и ООО «2050-Интегратор».- Руководитель проекта: Гинцяк А.М., заведующий лабораторией «Цифровое моделирование индустриальных систем» Центра НТИ СПбПУ
- Руководитель группы разработки: Успенский М.Б., к.т.н., научный сотрудник лаборатории «Промышленные системы потоковой обработки данных» Центра НТИ СПбПУ
- Руководитель группы аналитики: Бурлуцкая Ж.В., младший научный сотрудник лаборатории «Цифровое моделирование индустриальных систем» Центра НТИ СПбПУ
Соисполнители
- ООО «2050 Интегратор»
- ООО «Тетракуб»