VR training on a virtual gas pumping unit
A virtual reality (VR) application designed to facilitate the learning of procedures for handling gas pumping units (GPU) at compressor stations, with the potential for interactive engagement.
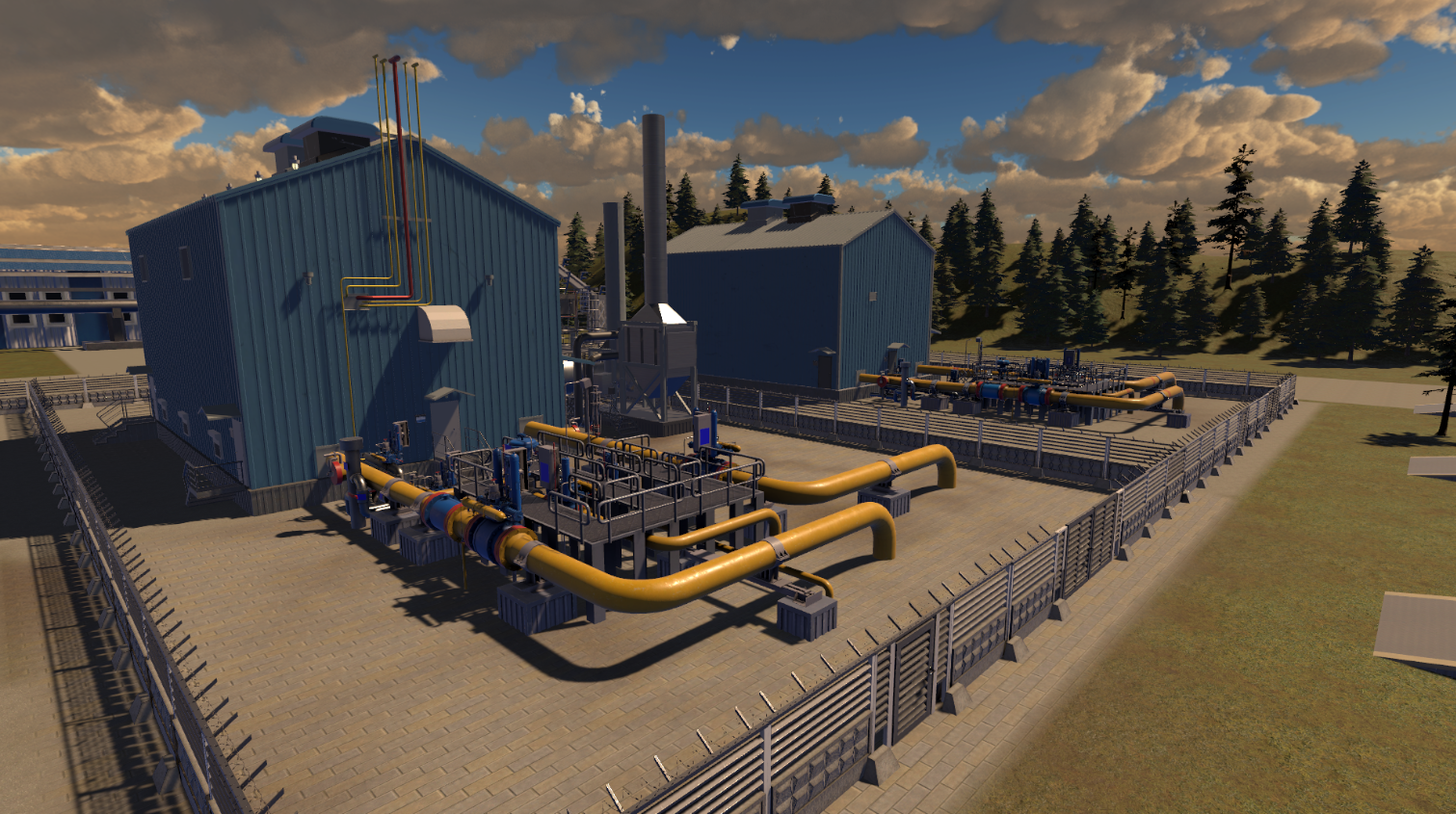
Task
The virtual training system ‘Maintenance, Troubleshooting, and Safety of Gas Pumping Units and Process Equipment’ was developed as part of the Programme for Improving the Quality of Education and Personnel Training of Gazprom PJSC/SPbPU.
The project aims to optimize the educational process in disciplines relevant to Gazprom PJSC at the Higher School of Power Engineering of the Institute of Energy, SPbPU.
The VR application has been developed to provide SPbPU students with the opportunity to gain hands-on experience in the safe and efficient operation of gas pumping units at compressor stations, in accordance with regulatory, technical, and occupational standards.
The virtual training system enables the simulation of operational, troubleshooting, and emergency scenarios at the compressor station gas pumping unit and auxiliary equipment (air coolers, separators, etc.).
The virtual model replicates a real Gazprom PJSC facility and adheres to the prevailing regulatory framework in all training scenarios. The training scenarios that have been implemented are designed to provide gas pumping unit operators and compressor station shift engineers with the skills required to perform their respective roles effectively.
Solution
The virtual training system comprises a three-dimensional model of a compressor station gas pumping unit, which is equipped with interactive control tools and a set of training programmes. These are designed to facilitate the effective training of students in GPU maintenance, troubleshooting, and on-site safety.
The prototype of the virtual station was one of the standard Taurus 60S gas pumping units (station number GPU-3) of the Severnaya compressor station (CS), which is part of the Northern Linear Gas Pipeline Production Department of Gazprom Transgaz Saint Petersburg LLC.
Three-dimensional models of the gas pumping unit were created using a virtual environment. These models were designed based on physical objects, including process piping, shut-off and control valves, blocks, nodes, and GPU parts. The text and illustrated descriptions, photo and video materials, and direct inspections of the complex were used to inform the software implementation of the virtual space. Typical scenarios of the maintenance of the GPU at the Severnaya CS were developed.
The creation of realistic three-dimensional models is achieved through the application of a substantial degree of detail. The entire GPU process equipment complex is presented in the virtual space, including a hangar with a gas turbine engine and a centrifugal compressor, a unit control centre, a fire suppression system, ventilation and heating systems, external pipelines of process and fuel gas and buffer air, and drainage pipelines. Next to the hangar there is an air intake bridge with an air-cooled oil cooler and a heat recovery system.
The VR training programmes are arranged according to the technological regulations, bypass routes, and operator's work algorithms of the real GPU-3 at Severnaya compressor station. The user operation scenarios were prepared by employees of the Higher School of Power Engineering of the Institute of Energy, SPbPU. They are designed to provide students with a comprehensive understanding of the duties and responsibilities associated with the role of a compressor unit operator, with a particular focus on the duties and responsibilities of a compressor station shift engineer. The monitoring system for task execution tracks and presents a visual representation of the process of executing a given scenario. In order to enhance the user experience of virtual reality, a sound system has been developed.
The software is designed to be used on multiple platforms. Two distinct versions of the software have been developed, one for use with a VR kit (including VR headsets and manipulators) and one for conventional personal computers with standard input devices (e.g., a keyboard and a mouse).
Project significance
The VR training system offers students the opportunity to develop their ability to follow instructions while also gaining an understanding of the mechanical, thermal, and gas-dynamic processes occurring in the equipment under various control actions. As virtual GPU operators, trainees will be able to comprehend the causal relationships between their actions and the equipment's reaction and subsequently determine the extent of deviation from the regulated state and the sequence of necessary actions.
The VR application facilitates remote learning, eliminates the risk of injury during training, reduces the time required for graduates to adapt to their new roles in Gazprom's divisions, and enhances the competitiveness of Politech graduates in the labour market.
Details
The scenarios encompass the regular bypass of the GPU on standby, the preparation of the GPU for launch, the launch of the GPU, the normal, accelerated, and emergency shutdown of the GPU, the operation of the warning alarm system and the personnel actions in case of its activation, the maintenance of the GPU and auxiliary equipment, and the procedure of actions in case of deviation from the norm of the allowed parameters in case of abnormal situations. Upon launching the software, each scenario generates a unique set of work situations.
Scenario examples
Scenario No. 1. Regular bypass of GPU on standby (hot standby)
Examine:
- Gas fire suppression system premises.
- Exhaust system, drainage reservoirs.
- Air intake bridge with an air-cooled oil cooler.
- Machine control centre premises
- GPU premises, GPU crane strapping.
Scenario No. 2. GPU preparation for the launch
- Internal and external GPU preparation
- External inspection and GPU crane strapping preparation
- Exhaust system preparation
- Fire suppression unit room inspection
- Check of the power supply circuit breakers in the machine control centre
- Change of the ‘Standby’ sign to a ‘Working’ sign
The student employs a virtual tablet to monitor activities, save activity reports, and rewind time while performing activities.
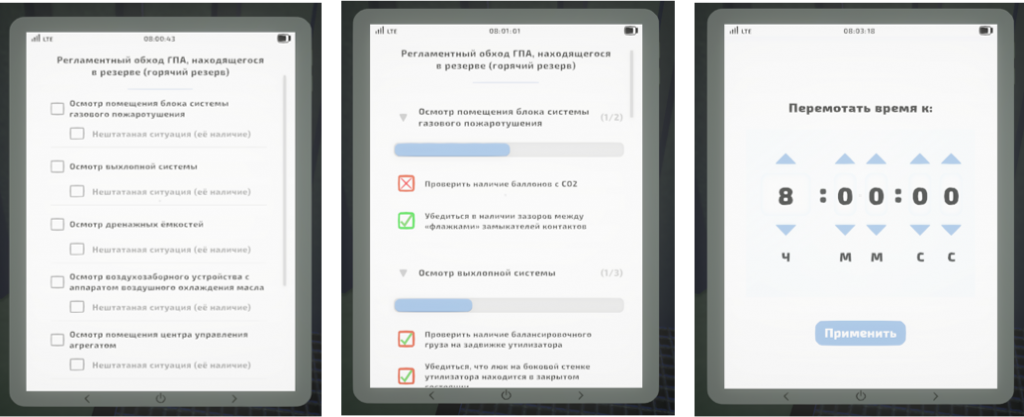
Technologies
3D Development Environment | Blender, Substance 3D Painter, Marmoset Toolbag |
Software Development Environment | Unity, Visual Studio, JetBrains Rider |
VR kits | HTC VIVE PRO, Oculus Rift S и другие гарнитуры, совместимые с OpenXR |
Programming languages and frameworks | С# |
Project team
- Industrial Systems for Streaming Data Processing Laboratory, AES, SPbPU
- Higher School of Power Engineering of the Institute of Energy of SPbPU
Project manager: M.V. Bolsunovskaya, Head of the Industrial Systems for Streaming Data Processing Laboratory at SPbPU
Consultant: A.A. Drozdov, Head of the ‘Investigation of Compressors, Pneumatic Systems, and Gas Compression and Processing Facilities’ scientific direction, Higher School of Power Engineering, Institute of Energy, SPbPU
Scenario developer: V.B. Semenovsky, PhD in Engineering, Associate Professor at the Higher School of Power Engineering of the Institute of Energy
Partners
- Gazprom PJSC, Gazprom Transgaz St. Petersburg LLC
- Higher School of Power Engineering of the Institute of Energy of SPbPU