Virtual balloon gondola
A virtual reality (VR) representation of a hot air balloon cabin for a renowned traveler.
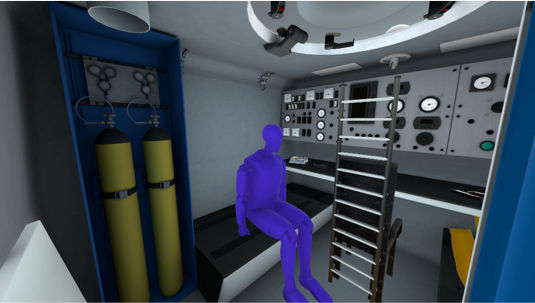
Task
In March 2024, the celebrated traveler Fyodor Konyukhov and Ivan Menyaylo are scheduled to undertake a balloon flight from the Murmansk region to Chukotka. The expedition will traverse a distance of over 5,000 kilometers, encompassing a range of challenging natural and climatic conditions. The balloon gondola design was developed by a team of students and engineers from the "Digital Engineering" Advanced Engineering School of SPbPU. The design was created using the world's best practices and considering the experience gained from other aerial expeditions. In 2016, Fyodor Konyukhov set a world record by flying a hot air balloon around the Earth in 11 days, 4 hours, and 20 minutes. The Morton hot air balloon, which has enabled the traveler to cover over 35,000 kilometers, was designed by the Morton Company. In order to achieve new aeronautical records, engineers from SPbPU AES developed a modernized gondola design. The ISSDP Laboratory was tasked with developing an interactive VR version of the gondola in order to shorten the time required for testing and refinement of the cabin.Solution
The gondola model was developed by students of the "Digital Engineering" Advanced Engineering School in cooperation with engineers of the "Computer Engineering Centre" (CompMechLab®) Engineering Centre, AES, SPbPU.
Fyodor Konyukhov presented the mandatory design requirements based on his own unique flight experience during his visit to the AES SPbPU in May 2023. In order to address the design issue, a team of AES SPbPU students was established, comprising members from the CompMechLab® Engineering Centre. The engineering team undertook a comprehensive analysis of the task at hand, formulated the requisite requirements, and developed detailed terms of reference for the engineering component of the project. In collaboration with engineers, students constructed mathematical and computer models, performed mathematical and computer modeling, conducted multivariate numerical tests, and developed working design documentation for the manufacture of a product from composite materials. Specific consideration was given to the design of a comfortable and secure handling system, as well as the implementation of soft landings, with the objective of ensuring the safety and comfort of the flight.
In selecting the optimal shape for the gondola, we determined that a square configuration in the horizontal plane would be the most effective. The gondola is equipped with additional protection in the form of reinforced corners at the lower extremities. This structural reinforcement serves two purposes: firstly, to absorb the impact of landing, and secondly, to act as an impact energy damper, thereby ensuring a soft landing and preventing injury to the passengers. In the event of a splashdown, certain structural features of the gondola's design will prevent it from capsizing.
The ISSDP Laboratory developed the VR application in two versions:
- Engineering version created in accordance with the technical documentation provided by CompMechLab® engineers;
- "Design" version of the model is aligned with the concepts of young designers, namely the winners of the federal competition "Young Design-2023" in the nomination "To the North!" established by the Advanced Engineering School of SPbPU.
The traveler was able to utilize VR visualization to gain a first-person perspective of the interior, assess the accessibility of the equipment located therein, evaluate the ergonomics of the cabin, and provide constructive feedback on potential enhancements.
Development stages
- A comprehensive 3D model of the gondola and detailed models of secondary objects (geometry creation, UV setting, and texturing) were created.
- The virtual scene was configured in accordance with the requisite specifications, including the precise placement of all models, the establishment of physical boundaries, and the light baking.
- The VR control mode was developed to facilitate interactivity with the environment, including object movement and actions with them. Additionally, operator logic was incorporated to enhance the user experience.
The VR application is presented in two versions: one utilizes the UNIGINE engine, and the other utilizes the Unity engine.
Technologies
3D development environment | Blender, Substance 3D Painter, Marmoset Toolbag |
Software development environment | Unity, UNIGINE, Visual Studio, JetBrains Rider |
VR-kits | HTC VIVE PRO, Oculus Rift S и другие гарнитуры, совместимые с OpenXR |
Programming languages and frameworks | С# |
Partners
- "Digital Engineering" Advanced Engineering School, SPbPU
- Computer Engineering Centre (CompMechLab®), AES, SPbPU
- Industrial Systems for Streaming Data Processing Laboratory, AES, SPbPU
Project Team
- VR Team Leader: A.A. Kuzmichev, Chief Project Engineer, Industrial Systems for Streaming Data Processing Laboratory, AES, SPbPU
- VR Team Tech Lead: A.O. Kuptsov, Lead Developer, Industrial Systems for Streaming Data Processing Laboratory, AES, SPbPU
- Engineering Team Leader: A.A. Mikhailov, Head of the Software Licensing and International Projects Department, Institute of Advanced Manufacturing Technologies, SPbPU
- Student group supervisor: M.V. Ivanov, Engineer at AES, SPbPU