Digital model of the hydraulic drive for lab sessions
The task is to develop a digital model of the hydraulic drive for students’ lab sessions involving hydraulics and hydraulic/pneumatic drive of machine mechanisms.
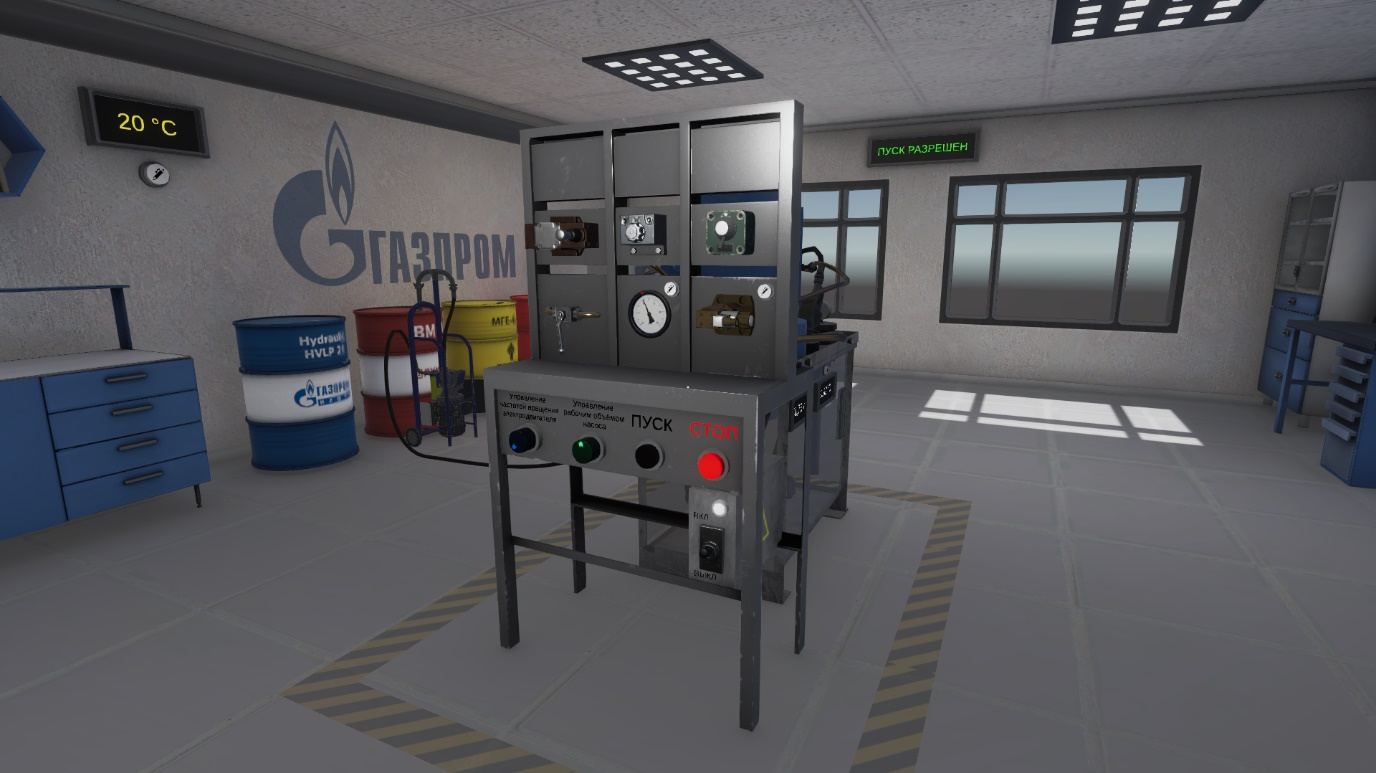
Task
Within the Education Quality Improvement and Personnel Training Programme (2021-2022) for Gazprom PJSC /Peter the Great St.Petersburg Polytechnic University (SPbPU), one of the main tasks on modernization of the laboratory facilities at Institute of Machinery, Materials, and Transport, SPbPU, is to develop a digital model of a hydraulic drive and scenarios for virtual lab session involving hydraulic equipment.
Digital lab sessions on hydraulics and hydraulic/pneumatic drive of machine mechanisms will allow teaching students more effectively within the "Ground Transportation and Technological Complexes" programme, which also includes planning, employment, and production of complex lifting equipment and conveyor belts used in pipeline construction.
Solution
Students complete lab sessions involving the hydraulic drive of material handling equipment using the program. They study how different grades of oil perform under pressure at certain outdoor and indoor temperatures.
The digital room of the hydraulic drive laboratory is fully equipped with a hydraulic drive, measuring devices, and oil drums.
The users must run the program, examine the equipment, choose the oil by the Russian producers of petroleum products required for lab session, then select the equipment for filling, and pump the oil into the tank of the test equipment. After proper preparation of the digital booth, the student gets permission to launch it. The oil tank starts to heat up, and the student adjusts the system pressure via sensors. All actions are recorded in a digital report, and the teacher checks them after the student completes the lab session.
Students receive various settings such as room temperature and volume, and the oil brand. Different task options make it impossible to cheat.
The project is based on the Unity3D real-time development platform. The digital booth model, authentic objects of the environment, and the room for lab sessions are made in Blender 3D editor. The program also contains all the interactive elements necessary to perform actions in a digital environment.
The project was implemented in several stages:
- Collection of references and sizes of real equipment for further 3D modeling;
- Creation of 3D models for reference and measurement;
- Creation of laboratory scenarios;
- Creation of the product's software logic;
- Combining 3D models and software logic.
As a result, a digital model of a hydrauic drive has been created. While using the model, the following actions can be performed:
- Hydraulic drive components' production labels examination
- Filling the oil tank with power fluid
- Hydraulic pump volume and hydraulic drive electric motor speed regulation
- Starting and stopping the hydraulic drive
- Pressure output control in hydraulic drive system
Technologies
Software programming languages and frameworks: | C# for Unity3D |
OS: | Windows 10 |
CVS: | Git, GitLab |
IDE: | Visual Studio 2022 |
Intellectual Property
Project team
- Project Manager: A.V. Ascheulov, Professor at Institute of Machinery, Materials, and Transport, SPbPU
- Development Team Lead: M.V. Bolsunovskaya, Head of the Industrial Systems for Streaming Data Processing Laboratory, NTI Center, SPbPU
- Tech Lead: N.M. Sherepa, Programmer of the Industrial Systems for Streaming Data Processing Laboratory, NTI Center, SPbPU
Students and professors of Institute of Machinery, Materials, and Transport, including ones at Institute of Computer Science and Technology, Higher School of Cyberphysical Systems & Control have also taken part in the development of digital models
Contractors
- Industrial Systems for Streaming Data Processing Laboratory, NTI Center, SPbPU
- Higher School of Cyberphysical Systems & Control, Institute of Computer Science and Technology, SPbPU