A novel methodology and apparatus for the automated assessment of bitumen adhesion to gravel have been devised for use in road construction
A joint venture between the Industrial Systems for Streaming Data Processing (ISSDP) Laboratory of the SPbPU NTI Center and Tetracube LLC, an industrial partner of the SPbPU NTI Center, has yielded the development and patenting of a hardware and software system (HSS) and methodology for automated assessment of the degree of adhesion of bitumen to gravel of different types.
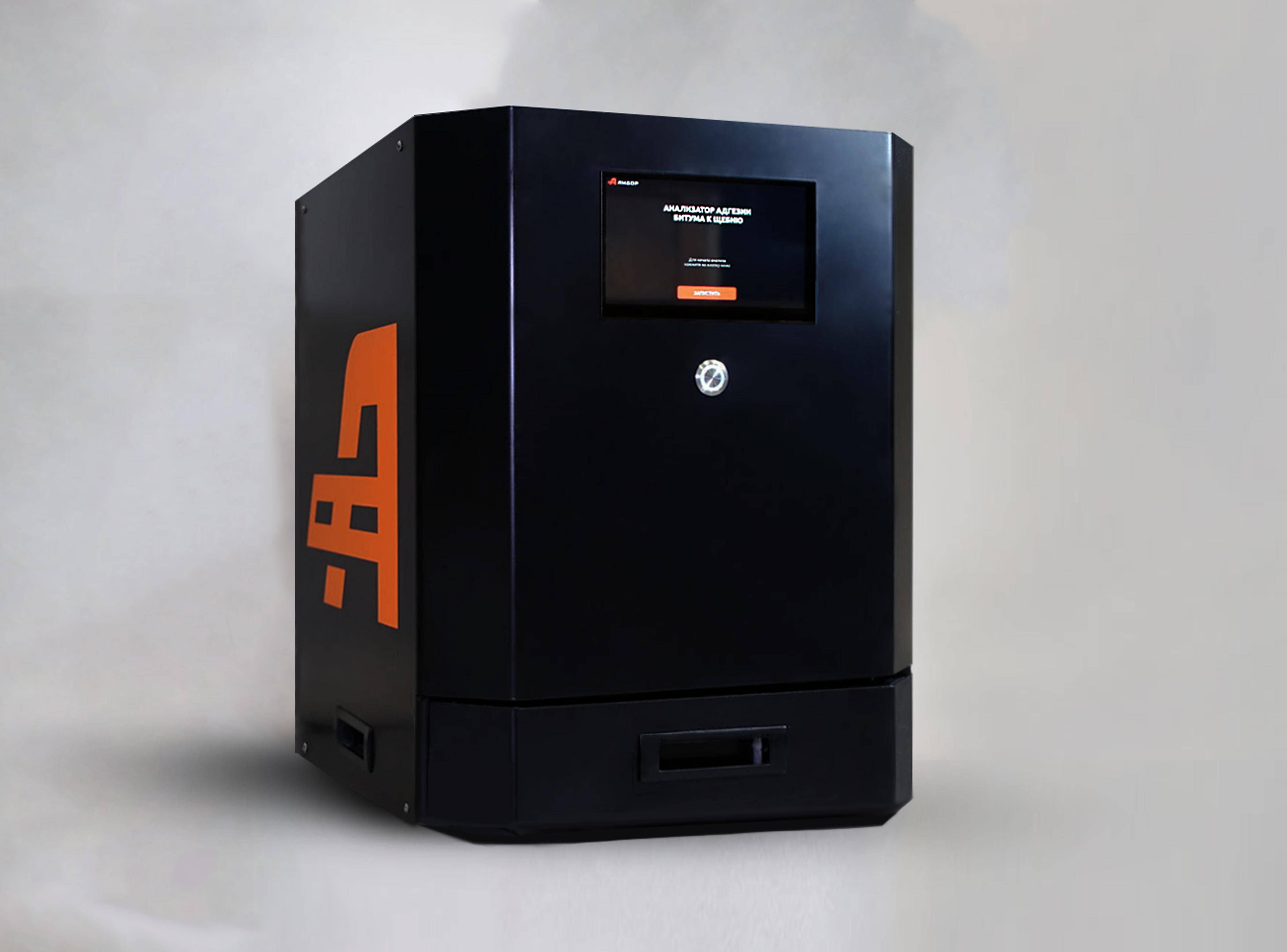
The development was conducted in collaboration with the customer, Amdor LLC, which is the largest manufacturer and supplier of chemical products for road construction in Russia.
The project resulted in the design of a device and the development of a methodology for the quantitative determination of the degree of adhesion of bituminous material to gravel. The analysis is based on the measurement of the area and thickness of the residual bitumen coating of gravel after tests simulating the loads that occur during the exploitation of roadways. The measurement is conducted through the use of photographic techniques, specifically the capturing of images of gravel samples, followed by a subsequent analysis of the digital images by means of computer vision technology.
The adhesion properties of bituminous binder are a critical determinant of the quality and durability of asphalt pavements. In accordance with the established regulatory documents, the initial tests are conducted by an expert who determines the adhesion properties of bitumen by visual assessment. The residual area of bitumen on gravel is evaluated as a percentage during the inspection of samples after testing by boiling (GOST R 58 406) or rolling bottle (EN 12697-11) methods. The developed HSS is capable of functioning with both methods, thereby enabling a notable reduction in the influence of human error when determining the extent of bitumen coating on gravel surfaces and a considerable enhancement in the precision of adhesion degree estimation.
In the tests conducted in accordance with the specifications set forth in EN 12697-11, gravel samples coated with bitumen and subjected to a curing process in a heat chamber are subsequently air-dried for a period of one hour. These samples are then placed in bottles containing distilled water. The bottles are numbered in sequence, sealed with waterproof caps, and placed on the rollers of the bottle rolling apparatus, which is manufactured by Frowaq (Germany). The rolling duration is 24 hours, plus or minus 10 minutes. Subsequently, grains of gravel coated with binder residues are washed with distilled water and laid out on silicone or paper napkins to prevent contact between grains.
Following a 1.5-2 hour exposure at room temperature and drying of the samples, they are placed in the sliding tray of the HSS in order to determine the degree of adhesion of the bitumen film.
When in a closed position, the device is capable of maintaining the requisite conditions for photography, namely the absence of external light sources and object reflections. The device acquires a digital image of gravel in a plane perpendicular to the lens axis and subsequently analyzes this image using software based on computer vision algorithms.
The margin of error associated with the visual estimation method ranges from 15 to 30%, whereas digital estimation techniques can reduce this error to a range of 2 to 5%.
‘For those in the road industry, this project could signify a departure from an era of standards that rely on subjective evaluation methods. The methodology under development is designed to yield highly accurate and reproducible test results while simultaneously reducing the impact of subjective factors. The HSS will assist consumers in making more objective selections of asphalt pavement materials, thereby reducing the likelihood of utilizing poor-quality components that could subsequently necessitate repair work.
At this juncture, a consortium of independent laboratories is engaged in testing, the results of which, at this preliminary stage, demonstrate compliance with the stated accuracy of determining the degree of bitumen adhesion to gravels of different types. The integration of the device and methodology with GOST R 58 406 is currently being finalized. The subsequent phase will entail the transfer of the device for pilot operation in the laboratories of the largest road construction companies. Should reports indicate a positive experience of utilizing the HSS, the subsequent step will be to consider the launch of mass production and incorporation of the device into the existing standards of adhesion testing. This will facilitate significant advancement in the practice of primary testing for asphalt quality,’ comments Alexander Boldyrev, Deputy CEO for Finance and Development of Amdor LLC.
The developed hardware and software system will unify the obtained data and facilitate the future creation of a digital database of studies from various sources. This will enable all specialists in the industry to compare results.
‘It is currently not feasible to obtain reliable results through the utilization of the available methods for the assessment of adhesion, due to the inherent limitations of these methods. Such assessments are contingent upon the specific conditions of the test and the potential for subjectivity in estimating the quantity of remaining bitumen. The presumed advantage of this technique in reducing the margin of error in test results is highly encouraging, and we eagerly anticipate the deployment of the equipment in our laboratory for preliminary testing. Furthermore, the equipment is capable of automatically creating a test database,‘ says Natalia Maidanova, PhD in Engineering, Deputy Director for Quality, Head of the Research and Development Center of JSC Asphalt Concrete Plant No. 1.
The device is portable (measuring 0.5 x 0.4 x 0.5 meters and weighing up to 16 kilograms), which makes it suitable for use in road construction laboratories and enterprises. The HSS’s relatively compact design allows for straightforward integration into the company’s existing instrument base, negating the need for additional space. Furthermore, the HSS can be moved between different locations with minimal effort.
To date, there are no complete analogues of the development on the market. The existing software solutions, both Russian and international, are used only in scientific laboratories and determine the area of bitumen coating of gravel with varying accuracy, which does not allow for the acquisition of a representative sample.
A utility model patent ‘Device for bitumen adhesion assessment’ was registered for this development. Authors: Boldyrev A.V., Kazakov D.V., Rakova V.V. Reg. No. 213922. Registration date: 04.10.2022. Copyright holder: Amdor LLC.